There are several difficulties in running a distribution center, particularly with the dispatch and delivery procedures. A well-structured dispatch system is crucial for satisfying client needs and cutting down on delays in today’s fast-paced industry. The dispatch and delivery procedure in a distribution center is explained in depth in this handbook, providing helpful advice. You will learn how a well-functioning process may enhance operations, save expenses, and boost consumer confidence by reading this guide. The guide is written in simple language and arranged in a clear structure to help you easily follow along.
Why an Effective Dispatch and Delivery Process Matters
Before diving into the details, it is important to understand the role that an efficient dispatch and delivery system plays in the success of a distribution center. The following points highlight its significance:
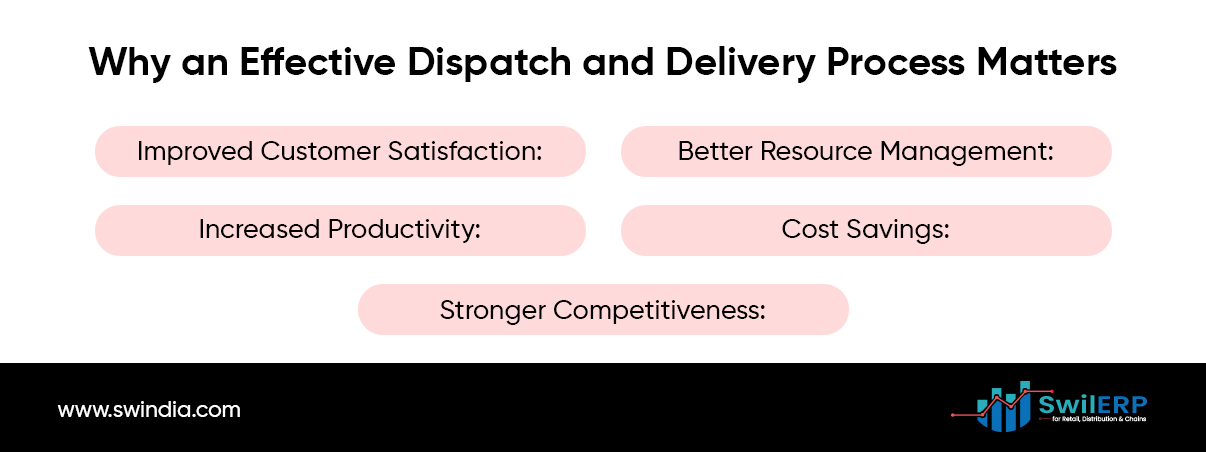
- Improved Customer Satisfaction: Quick and reliable deliveries keep customers happy.
- Better Resource Management: An organized process helps reduce waste of time and resources.
- Increased Productivity: When each step is clearly defined, the overall work moves faster.
- Cost Savings: Fewer delays and errors can save money on labor and transportation.
- Stronger Competitiveness: With smooth operations, the distribution center can meet tight delivery deadlines and customer expectations.
Overview of the Dispatch Process
The dispatch process is the set of activities that occur from the time an order is ready until it leaves the warehouse. Below is an overview of the main steps:
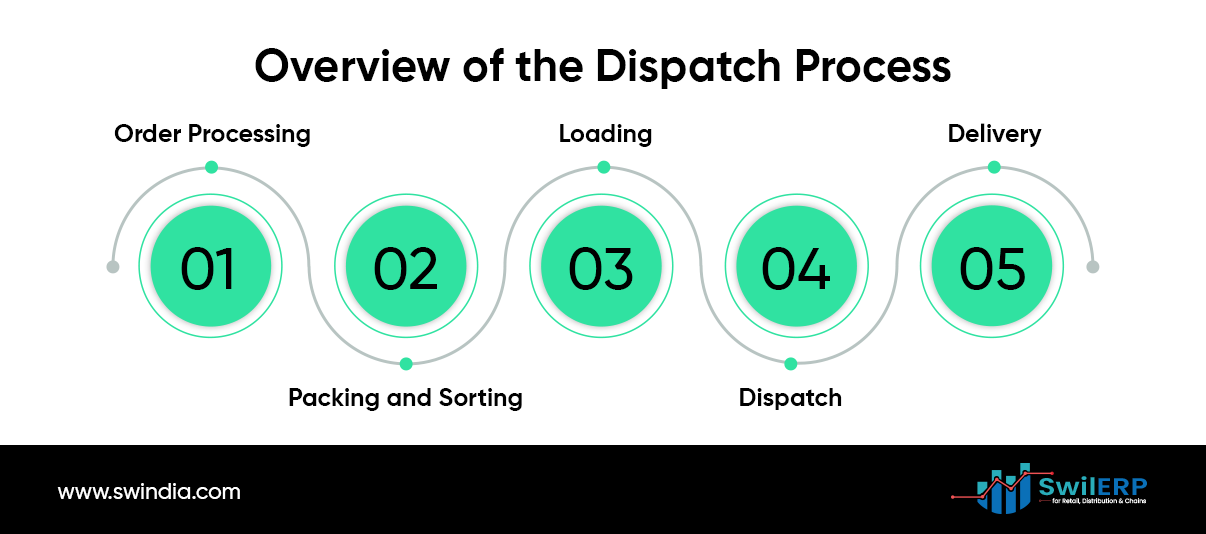
Order Processing:
- Orders are received either from an online system or through phone/fax.
- They are confirmed and processed by staff.
Packing and Sorting:
- Items are gathered from storage areas.
- Orders are packed securely and marked for delivery.
- Sorting is done to group orders based on delivery routes.
Loading:
- Packed orders are loaded onto delivery vehicles.
- The loading process follows a planned route to ensure minimal handling.
Dispatch:
- Vehicles leave the facility at designated times.
- Dispatch logs are maintained for accountability.
Delivery:
- Orders are delivered to customers.
- Delivery personnel follow a specific route to cover all locations.
- Feedback is collected to ensure a successful handover.
Each of these steps is important and, if managed well, contributes to an efficient overall process.
Key Components of a Dispatch System
A distribution center’s dispatch system relies on multiple critical components that work in unison. Understanding these parts can help streamline the entire process:
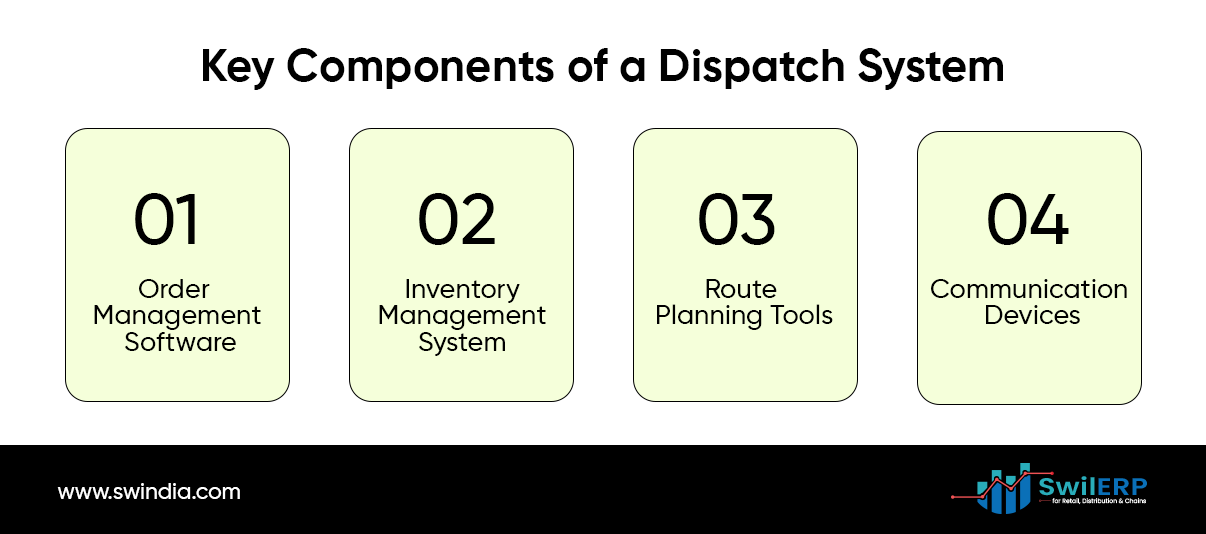
1. Order Management Software
Software that manages orders is central to the dispatch process. It keeps track of orders, monitors stock levels, and updates customer information in real-time. The software automatically flags orders that need immediate attention and helps in scheduling deliveries.
Features to look for:
- Real-time updates
- Integration with online sales platforms
- Easy search and reporting features
2. Inventory Management System
It is essential that the inventory management system works hand-in-hand with order management. A good system can tell you which items are available, in which quantity, and where they are located within the center.
Important functions:
- Barcode scanning for quick item retrieval
- Automated reorder levels
- Visibility across multiple storage zones
Read also: Warehouse Inventory Management with FIFO and ABC Analysis
3. Route Planning Tools
Efficient route planning reduces transit time and fuel costs. This tool uses data such as order destination, traffic conditions, and delivery windows to create the best possible delivery routes.
What to expect:
- Optimization for multiple stops
- Real-time traffic updates
- Ability to reroute in case of emergencies
Read also: AI-Driven Route Optimization in Delivery Management
4. Communication Devices
Reliable communication is essential between the dispatch team and delivery personnel. Use mobile devices, radios, or messaging apps to relay important updates and handle urgent queries during deliveries.
Best Practices for Running an Effective Dispatch and Delivery Process
To achieve a seamless operation, you should adopt several best practices that address each step in the dispatch process.
Clear Standard Operating Procedures (SOPs)
Developing and maintaining well-documented SOPs is the foundation of a consistent process. Every employee, from the order processor to the delivery driver, should have a clear understanding of their responsibilities.
What to include:
- Step-by-step instructions for each task
- Guidelines for handling exceptions
- Checklists for packing, sorting, and loading
Training and Skill Development
Employees must be well-trained not only in individual tasks but in how the entire process works. Regular training sessions can help staff members understand new technologies and processes.
Tips for effective training:
- Hands-on workshops and simulations
- Frequent refresher courses
- Access to updated manuals and guidelines
Regular Audits and Performance Reviews
Conducting regular audits helps identify inefficiencies or errors in the dispatch process. Performance reviews, both individual and system-wide, can highlight areas for improvement.
Audit focus areas:
- Accuracy of order fulfillment
- Timeliness of dispatch and delivery
- Feedback from delivery personnel
Embracing Technology and Automation
Modern solutions like automation and robotics can greatly improve dispatch efficiency. Technologies such as automated conveyors, robotic sorters, and real-time tracking systems can reduce manual errors and improve throughput.
Consider these innovations:
- Automated packaging and labeling machines
- Mobile apps that provide real-time updates to drivers
- Cloud-based systems for integrated data management
Read also: Smart Warehouse Tools: RFID, Barcode, WMS
Maintenance of Equipment and Infrastructure
Regular maintenance of all equipment used in the dispatch process is crucial. This includes everything from forklifts and scanning devices to computers that run the management software. A well-maintained fleet and infrastructure prevent breakdowns and delays.
Maintenance checklist:
- Scheduled servicing of vehicles and machinery
- Regular inspection of storage systems
- Software updates and hardware checks
Challenges in the Dispatch and Delivery Process
While an efficient system has many benefits, there are common challenges that businesses face in this arena. Addressing these challenges head-on can prevent setbacks.
Human Error
Even with automated systems in place, human error remains a challenge. Mistakes such as incorrect picking, mislabeling, or improper loading can disrupt the entire process.
Mitigation strategies:
- Double-checking procedures
- Simple and clear checklists
- Extra training sessions focusing on error-prone areas
Delays Due to External Factors
External elements, such as traffic conditions, weather changes, or road construction, can impact delivery times. While you cannot control these factors, having contingency plans is essential.
How to manage delays:
- Use real-time route planning tools that adjust for traffic.
- Inform customers in advance if a delay is expected.
- Maintain a buffer time in delivery schedules.
Coordination Between Teams
Smooth coordination between the dispatch team, warehouse staff, and delivery drivers is necessary. When communication breaks down, the entire process is affected.
Improvement measures:
- Regular team meetings to discuss issues and solutions.
- A centralized communication platform accessible to all team members.
- Clear escalation procedures for any issues that arise during the day.
Technology Glitches
Systems can experience downtime or software bugs, which can delay processes. Even a well-integrated system can face challenges when updates or maintenance occur at inconvenient times.
Preventive measures:
- Regular software testing and updates.
- Backup procedures for manual processing during outages.
- Dedicated technical support that can resolve issues promptly.
How to Create a Culture of Continuous Improvement
A key factor in running a successful dispatch and delivery process is the commitment to continuous improvement. This means always looking for small changes that lead to better performance.
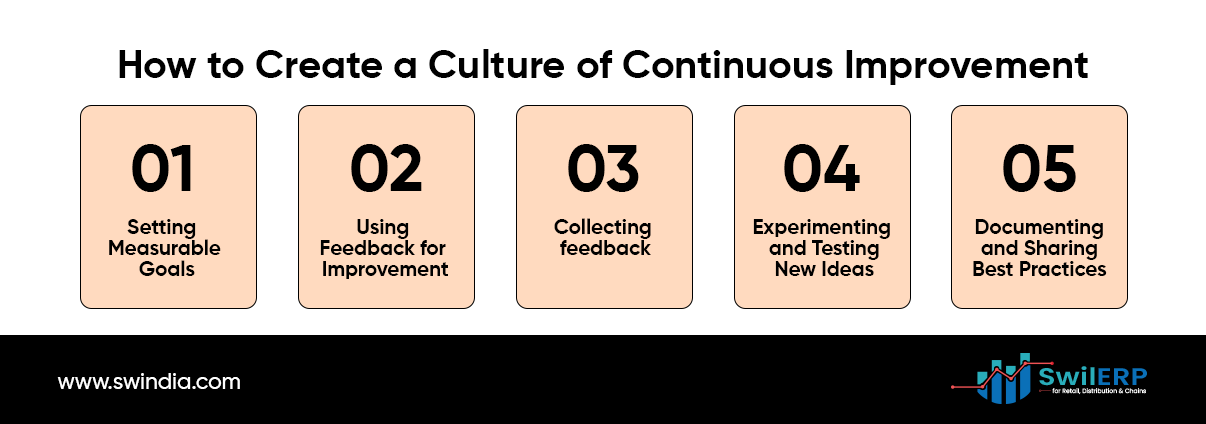
Setting Measurable Goals
Start by defining clear, measurable goals for the dispatch process. This might include targets such as reducing delivery times by a certain percentage or lowering the number of errors per shift.
Examples of goals:
- Reduce order processing time by 15% within six months.
- Lower shipping errors by 10% through improved training.
- Increase on-time deliveries by 20% by optimizing routes.
Using Feedback for Improvement
Feedback from both customers and employees is vital. Surveys, direct interviews, and even informal discussions can highlight issues that might not be apparent from data alone.
Collecting feedback:
- Use short online surveys after each delivery.
- Hold monthly staff meetings to discuss common issues.
- Monitor social media and customer reviews for insights.
Experimenting and Testing New Ideas
Try out new methods or technology solutions on a small scale before rolling them out company-wide. Small pilots can often uncover potential problems without disrupting the entire operation.
Pilot suggestions:
- Test a new packing method on one shift.
- Experiment with a new routing tool in a limited area.
- Gradually introduce automation in high-impact areas.
Documenting and Sharing Best Practices
As you implement improvements, document what works and share these practices with your team. A shared knowledge base ensures that good ideas are not lost and can benefit the entire organization.
Documentation tips:
- Maintain a digital log of all process changes.
- Use internal newsletters or meetings to share updates.
- Create a repository of instructional videos and manuals.
The Human Element in Dispatch and Delivery
Technology and processes are important, but the human element is the heart of any operation. The skills, attitudes, and dedication of your team can make a significant difference.
Building a Skilled Team
Invest in hiring people who are detail-oriented and motivated to work in a fast-paced environment. The right team can help overcome many challenges inherent in the dispatch process.
Key qualities to look for:
- Attention to detail
- Ability to follow procedures diligently
- Good communication skills
- Adaptability to new systems and processes
Encouraging Accountability
A culture where each team member takes responsibility for their part of the process can lead to fewer errors and a smoother operation. Accountability is not about blame but about continuous learning and improvement.
How to foster accountability:
- Set clear role definitions and expectations.
- Use performance metrics to track individual progress.
- Recognize and reward improvements and good performance.
Promoting Team Communication
Strong communication helps reduce missteps. Encourage open dialogue, where team members can report issues and suggest improvements without hesitation.
Communication methods:
- Daily briefings and end-of-day reviews.
- Instant messaging channels for real-time updates.
- Regular one-on-one meetings to address individual concerns.
Bringing It All Together
An effective dispatch and delivery process in a distribution center is built on clear systems, the right technology, and a dedicated team. When every part of the operation works together, delays decrease and customer satisfaction rises. Businesses must invest in training, technology, and continuous monitoring to achieve consistent results.
Key Steps to Success
- Implement a Unified Order and Inventory Management System:
Keep data up-to-date in real time to avoid mishaps.
- Adopt Reliable Route Planning and Communication Tools:
Minimize delays by planning the best routes and keeping open lines of communication.
- Focus on Employee Training:
Regular training sessions help reduce human error and boost morale.
- Set Measurable Goals and Monitor Progress:
Use data-driven insights to guide your continuous improvement efforts.
- Build a Culture of Accountability and Open Communication:
Encourage your team to speak up, share ideas, and learn from mistakes.
Final Thoughts
The dispatch and delivery procedures used by a distribution center are essential to both client happiness and the general performance of the company. From order processing to final delivery, your business may function efficiently by using best practices and resolving frequent issues. Faster delivery are only one advantage of an integrated system; other advantages include reduced expenses, increased employee satisfaction, and an improved overall client experience.
To remain competitive, invest in technologies that help you manage orders, track inventory, and plan delivery routes with precision. Regular training, open communication, and ongoing growth are vital to overcome the hurdles that may occur.
Running a successful dispatch and delivery process is not an overnight task. It calls for consistent work, the appropriate tactics, and the flexibility to adapt to new difficulties. With the appropriate system in place and a focus on continual improvement, your distribution center may become a model of operational excellence.
If you found this guide helpful, consider reviewing your current dispatch process. Start by looking at each of the aforementioned areas and determining what aspects of your facility might want improvement. Stay tuned for further insights on managing and optimizing distribution center operations in our forthcoming posts.
This concludes our comprehensive guide to running a dispatch and delivery process in a distribution center. By following these steps and practices, you can build an efficient system that meets customer expectations and supports your business growth.