Creating the best warehouse layout is a key part of running a successful storage and distribution business. A well-planned warehouse helps things run smoothly, makes work easier, and saves money. This guide will walk you through the main steps and ideas for making a good warehouse layout.
1. Understand Warehouse Functions and Objectives
Before you start planning your warehouse layout, it’s important to know what your warehouse needs to do and what you want to achieve.
What’s your goal?
First, think about what your warehouse is mainly for. Is it just for storing things? Is it for sending out products to customers? Or is it to support a factory? Knowing this will help you make the right choices for your layout.
Evaluating Your Needs
Next, look at what kinds of things you’ll be storing, how much stuff will be coming in and going out, and if you might need more space in the future. This information will help you plan for the right amount of space and the right kind of storage.
Workflow Optimization
Try to make the way things move around your warehouse as quick and easy as possible. You want to avoid places where things might get stuck or slow down, and make it easy for workers to pick, pack, and ship items.
2. Plan Warehouse Zones
A good warehouse layout has different areas for different tasks. Here are the main zones you should think about:
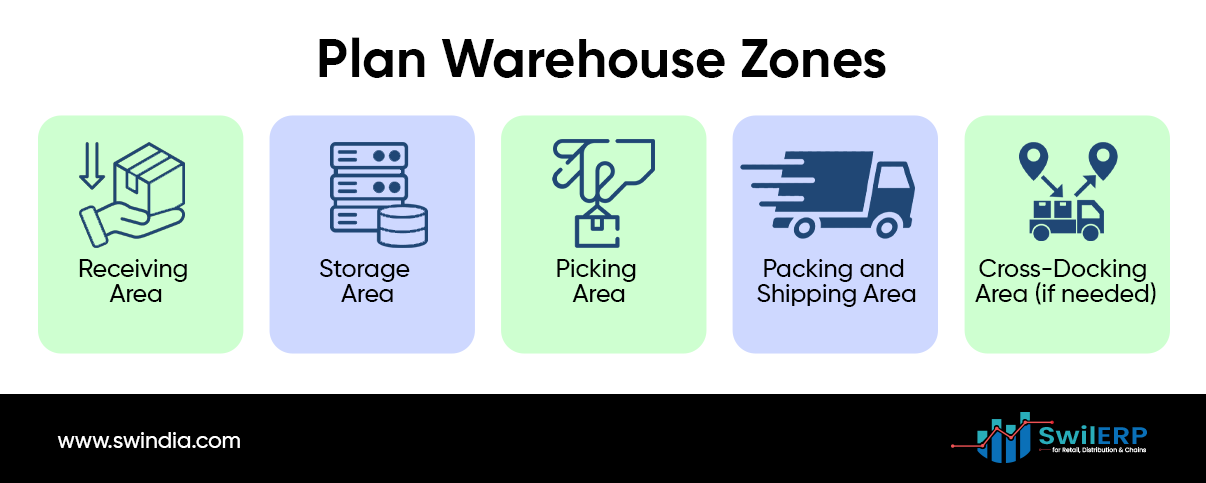
Receiving Area
This is where new items come into your warehouse.
Objective: Handle incoming goods quickly and easily.
Design Consideration: Put this area near the entrance with enough doors for trucks. Make sure there’s space to check the quality of new items and to put them somewhere temporarily.
Storage Area
This is where you keep your inventory until it’s needed.
Objective: Use space well for storing items while making sure they’re easy to get to.
Design Consideration: Choose the right kind of shelves or racks based on what you’re storing and how often you need to move it. Put items that are often needed in easy-to-reach places.
Picking Area
This is where workers collect items for orders.
Objective: Make order fulfillment faster.
Design Consideration: Put popular items in the middle where they’re easy to get to. Plan a logical path for workers to follow when they’re picking items.
Packing and Shipping Area
This is where orders are prepared to be sent out.
Objective: Make getting orders ready and shipping them out easier.
Design Consideration: Put this area near the doors where trucks will pick up orders. Make sure there’s enough room for packing stations, putting on labels, and checking orders before they’re loaded.
Cross-Docking Area (if needed)
This is for items that go straight from incoming trucks to outgoing trucks without being stored.
Objective: Handle goods that don’t need to be stored for long.
Design Consideration: Put this area close to both incoming and outgoing truck areas to make moving items easier.
3. Maximize Space Utilization
Using your warehouse space well is critical. Here are some ways to do that:
Vertical Space
Use tall shelves or racks to make the most of the height in your warehouse.
Aisle Width
Find a balance between narrow aisles (which give you more storage space) and wide aisles (which make it easier for forklifts and other equipment to move around).
Modular Design
Plan areas that can be changed easily as your inventory levels go up and down.
Mezzanines
Think about adding extra floors above the ground level for more storage or office space without making your warehouse bigger.
4. Ensure Efficient Material Flow
The way items move through your warehouse is significant. Here are some tips:
Flow of Goods
Design your layout so items move in a logical way from when they arrive to when they’re stored, then picked, and finally shipped out. Try to avoid having items cross paths or go back and forth.
One-Way Flow
If possible, make traffic go in one direction to avoid jams and make operations smoother.
Ergonomic Considerations
Make sure work areas, shelves, and picking systems are set up in a way that’s comfortable for workers. This helps reduce tiredness and injuries.
5. Use Technology to Optimize Layout
Using the right technology can make your warehouse work much better:
Warehouse Management System (WMS)
Use a computer system to keep track of where items are, how much you have, and the best routes for picking items.
Automation
Think about using machines to store and retrieve items or move them around. This can make things faster and reduce mistakes.
Barcode/QR Code Systems
Use barcodes or QR codes that can be scanned quickly to keep track of items accurately.
6. Plan for Safety and Accessibility
Safety is significant in a warehouse. Here’s how to include it in your layout:
Clear Aisles
Keep paths clear for forklifts, pallet jacks, and workers to move safely and quickly.
Emergency Exits
Make sure exit doors are easy to get to and clearly marked.
Signage
Use clear signs to show where things are, direct traffic, and remind people about safety rules.
Lighting
Make sure the warehouse is well-lit so people can work safely and find items easily.
7. Optimize Loading and Unloading Areas
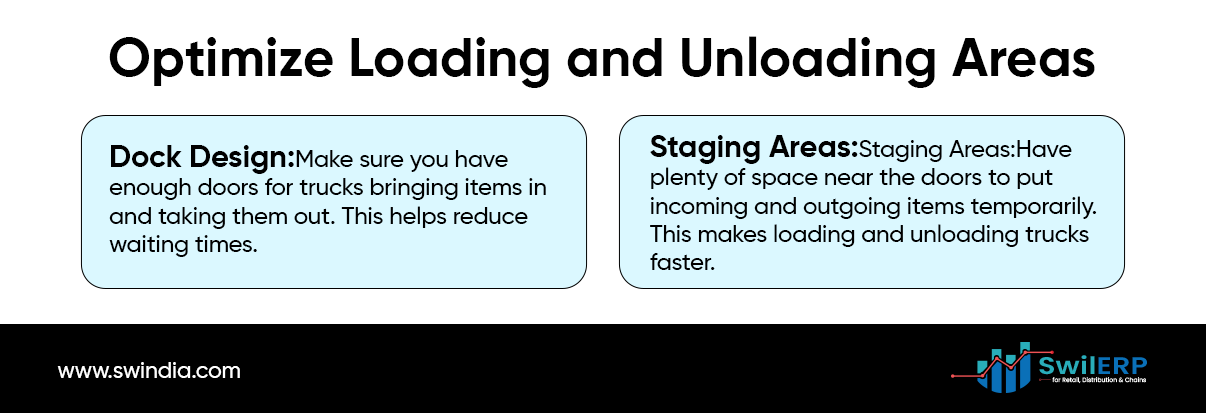
The areas where trucks load and unload are essential:
Dock Design
Make sure you have enough doors for trucks bringing items in and taking them out. This helps reduce waiting times.
Staging Areas
Have plenty of space near the doors to put incoming and outgoing items temporarily. This makes loading and unloading trucks faster.
8. Consider Future Growth
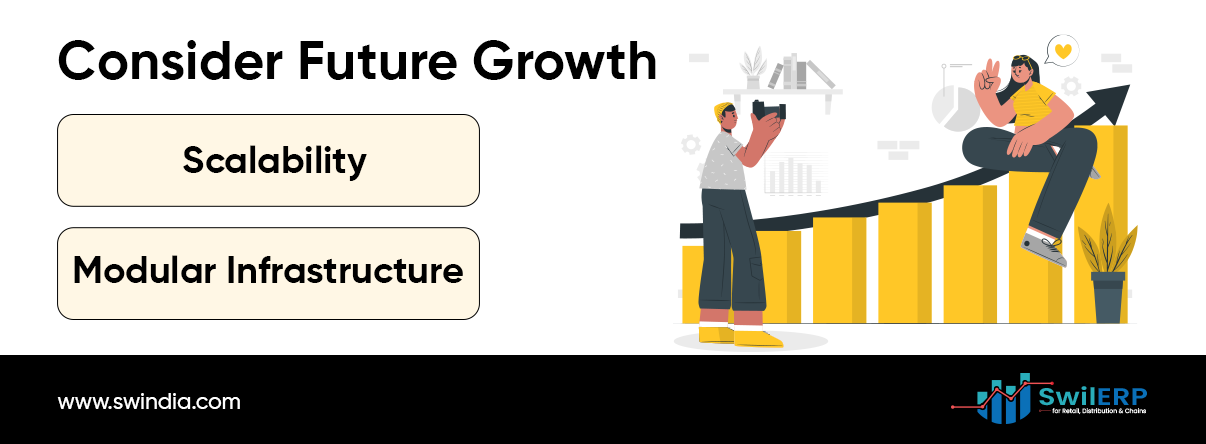
When planning your layout, think about how your business might grow:
Scalability
Design your layout so you can add more storage, machines, or loading areas as your business gets bigger.
Modular Infrastructure
Make sure you can add new areas easily without messing up the way things already work.
How to Design the Ideal Warehouse Layout
Now that we’ve covered the main parts of a good warehouse layout, let’s look at how to put it all together:
1. Understand Warehouse Operations and Needs
Before you start designing, you need to know exactly what your warehouse needs to do:
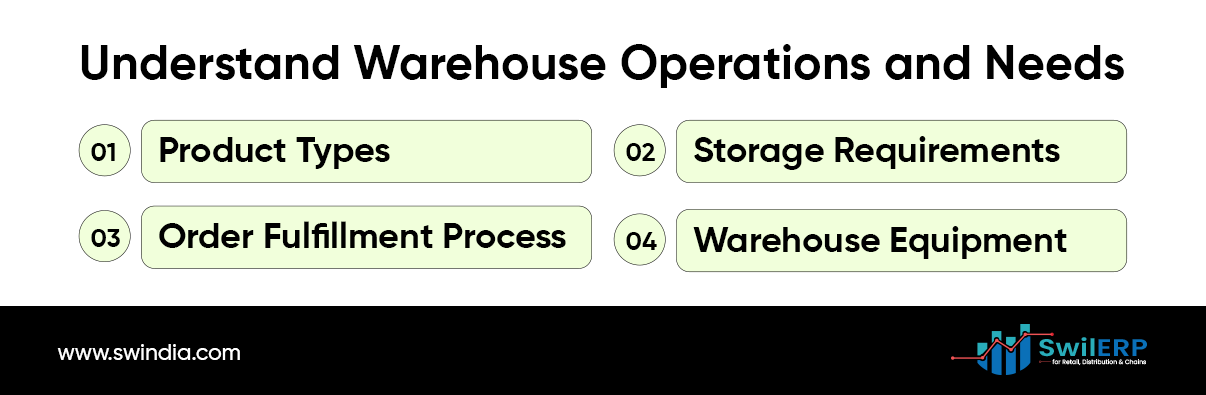
– Product Types: Think about how big and heavy your items are and if they need special care (like if they can go bad or break easily).
– Storage Requirements: Decide if you need special storage conditions, like keeping things cold or storing dangerous materials safely.
– Order Fulfillment Process: Figure out how you’ll pick orders and how often you’ll need to get to different products.
– Warehouse Equipment: Think about what kind of shelves, racks, and moving equipment (like forklifts) you’ll use.
2. Key Elements of Warehouse Layout Design
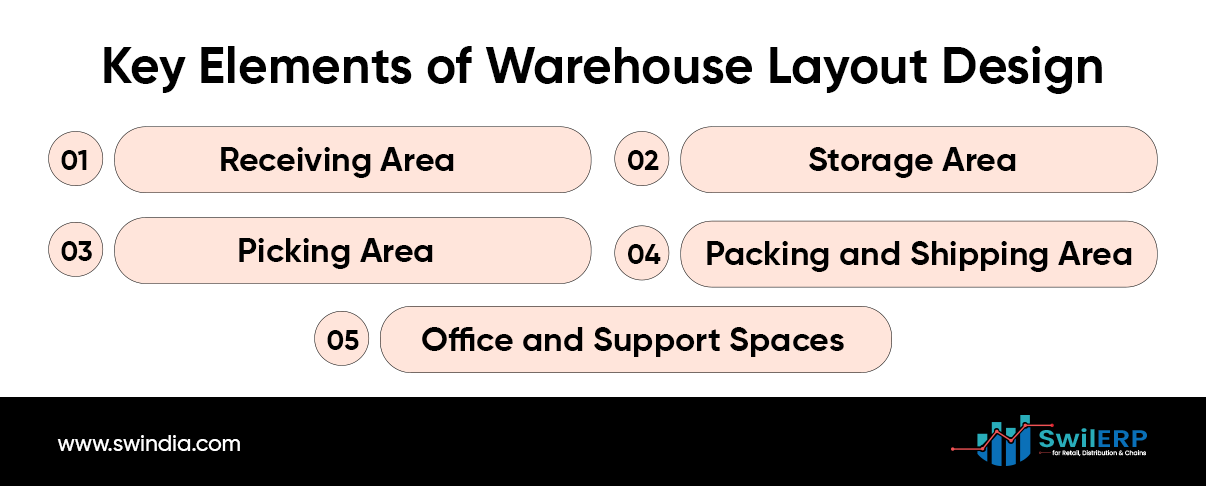
Here are the main parts you need to include when designing your warehouse:
– Receiving Area:
– Put this close to where trucks unload.
– Have enough space to check new items and sort them.
– Make sure there’s a clear path from here to where you’ll store things.
– Storage Area:
– This is the biggest part of your warehouse.
– Choose the right kind of storage (like different types of shelves or racks) based on what you’re storing.
– Put things that sell quickly in easy-to-reach places.
– Picking Area:
– Make it easy to get to popular items.
– Set things up so workers don’t have to bend or reach too much.
– Have different areas for picking small items and big items.
– Packing and Shipping Area:
– Put this close to where orders are picked.
– Make sure there’s enough room to pack orders, put on labels, and check quality.
– The shipping area should be near where trucks will load.
– Office and Support Spaces:
– Include areas for office work, break rooms, and safety areas like first aid rooms.
– Have a place to fix warehouse equipment.
3. Consider Warehouse Layout Types
Choose a layout that fits how you want things to move in your warehouse:
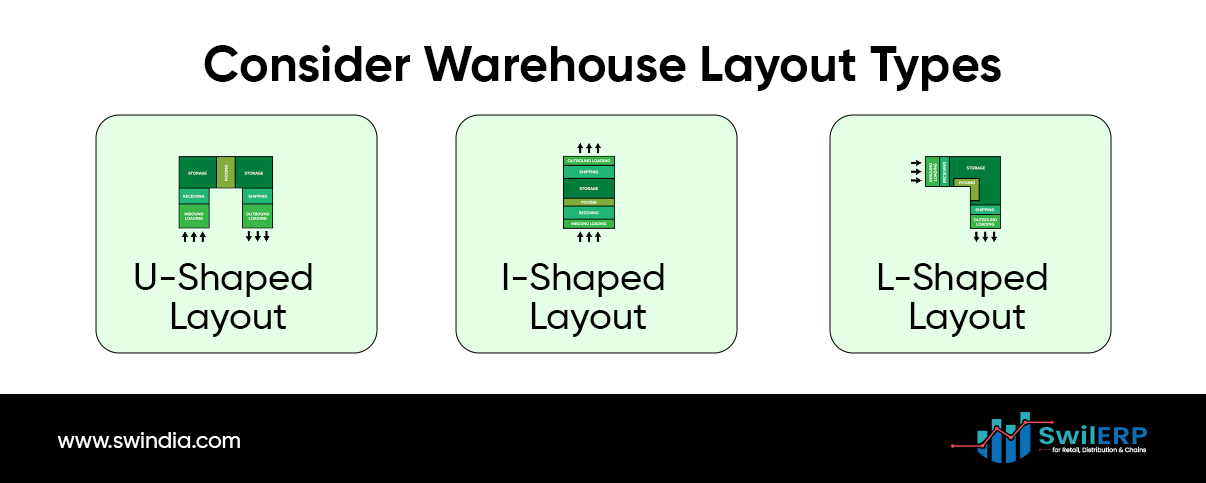
– U-Shaped Layout:
– Things move in a U shape from receiving to shipping.
– This works well for warehouses that move a lot of products quickly.
– I-Shaped Layout:
– Receiving is at one end, shipping at the other, with storage in the middle.
– Good for moving things directly from incoming to outgoing trucks.
– L-Shaped Layout:
– Receiving and shipping are on two sides that meet, forming an L shape.
– Works well if you don’t have much space or have special needs.
4. Plan the Flow of Materials and Traffic
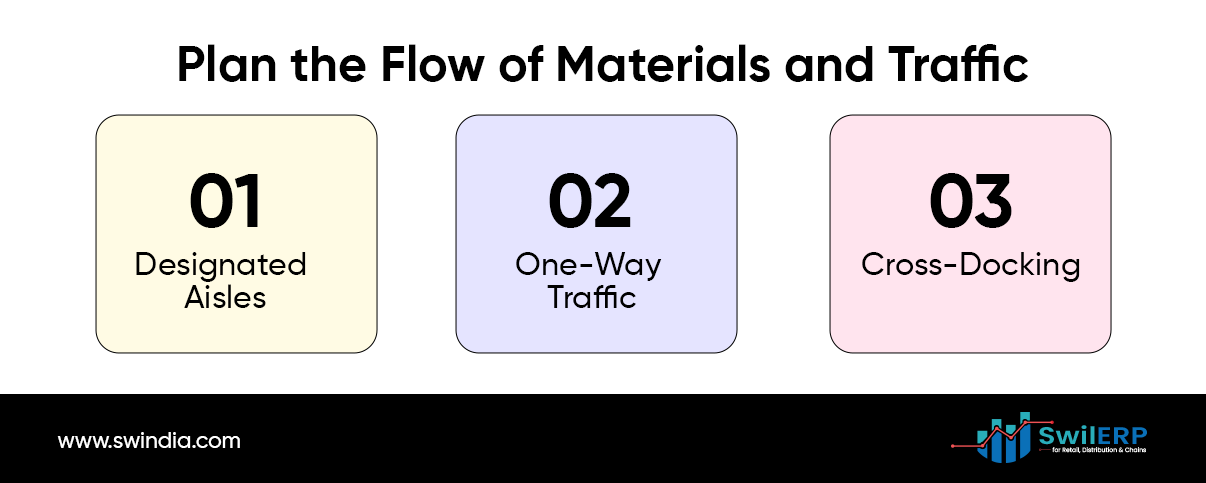
Design your layout so things and people can move around easily:
– Designated Aisles:
– Make aisles wide enough for forklifts and other equipment.
– Have separate aisles for picking items and for restocking.
– One-Way Traffic:
– In busy areas, make traffic go one way to avoid jams and make things safer.
– Cross-Docking:
– If you move a lot of products quickly, consider an area where you can move things directly from incoming to outgoing trucks.
5. Optimize Storage Solutions
Choose the right way to store things based on what you’re storing:
– Pallet Racking:
– Good for storing big, heavy items on pallets.
– You can choose different types based on how you need to access items.
– Shelving Units:
– Best for smaller items that workers need to pick individually.
– Use shelves that can be changed as your needs change.
– Vertical Storage Solutions:
– Use tall racks or machines that lift items up and down to use all your vertical space.
– Mezzanine Systems:
– If you’re short on floor space, add extra floors above for more storage or work areas.
6. Implement Safety Measures
Safety is essential in warehouse design:
– Clear Aisles and Signage:
– Keep all paths clear and wide enough.
– Use clear signs to show where to go and where safety equipment is.
– Safety Barriers:
– Put up barriers around busy areas to prevent accidents.
– Proper Lighting and Ventilation:
– Make sure the warehouse is well-lit and has good air flow.
7. Plan for Scalability and Flexibility
Your warehouse should be able to grow and change with your business:
– Modular Layout Design:
– Design so you can add more storage or work areas as you grow.
– Flexible Storage Solutions:
– Use shelves and racks that can be adjusted for different sized items.
– Future-Proofing with Automation:
– Think about how you might use robots or other machines in the future to make work easier.
8. Utilize Warehouse Management Systems (WMS)
Use a computer system to help manage your warehouse:
– Real-Time Inventory Tracking:
– Use a system that can tell you exactly what you have and where it is at any time.
– Pick Path Optimization:
– Use the system to figure out the fastest way for workers to collect items for orders.
– Integration with Automation:
– If you use machines to store or move items, make sure your computer system can work with them.
9. Map and Visualize the Layout
Before you build or change anything, make a detailed plan:
– Mapping Tools:
– Use computer programs to draw out your warehouse and see how things will move around.
– Mock Trials:
– Tryout your layout by walking through it or using toys to represent items and see if it works well.
Conclusion
Designing a good warehouse layout takes careful planning. You need to think about what your warehouse needs to do, how to use space well, how to make work easy and safe for people, and how your business might change in the future. By thinking about all these things and using the right tools and systems, you can create a warehouse that works well, saves money, and helps your business grow.